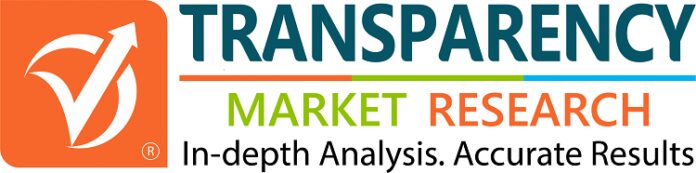
The global packaging industry was valued at ~US$ 908 billion in 2017. Constant advancements and innovations are shaping the future of pharmaceutical packaging technology. The vials market is estimated to reach ~US$ 9.6 billion by the year 2027. With high growth potential of the market, manufacturers are innovating on blow fill seal (BFS) vials, adopting measures that tackle counterfeit products, and developing two-in-one prefilled vial designs. Nano-printing allows invisible printing on vials that provide excellent security to combat counterfeiting. Two-in-one vials enable less chances of contamination, and serve as a cost-effective option as compared to traditional glass vials.
Manufacturers are driving innovation in the space of ophthalmic packaging. They are developing two-color injection-molded vials with a luer-lock closure and rubber stopper for ophthalmic liquids that require a calibrated dose. With advancements in the materials and equipment in this landscape, manufacturers are developing child-resistant and tamper-evident packaging that is well-suited for preservative-free formulations. These attributes of vials ensure seal integrity with the help of hot blowing, hot crimping, and cold crimping methods.
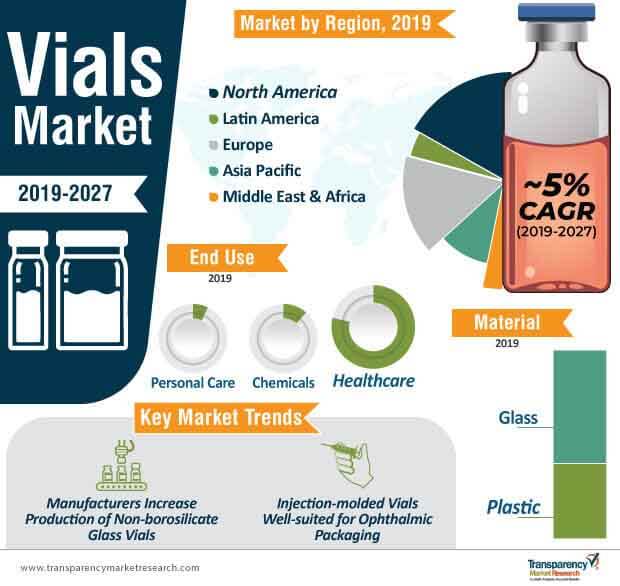
To understand how our report can bring difference to your business strategy, Ask for a brochure
Market Players Increase Expertise for Superior Chemical Resistance with Modular Product Offerings
There has been increasing demand for improved recovery and sensitivity of high- and low-concentrated biological and chemical formulations. This demand is rising as biomolecule sample loss is a problem at low concentrations. Also, non-specific binding and ionic interactions in formulations lead to loss at high concentrations. This is why, manufacturers are developing vials that protect these formulations, which aid in improved analytical results for healthcare providers.
Request a sample to get extensive insights into the Vials Market
The concept of ready-to-use products is surfacing in many pharmacies across the globe. This concept primarily caters to ready-to-mix formulations that do not require traditional compounding with a syringe and needle. Manufacturers are also leveraging drug stability in vials without the need for coatings in low-fill applications. This serves as an efficient and cost-competitive fill and finish for consumers, which is achieved through process optimization and improved dimensions for excellent quality and strength in vials.
Boron-free Glass and Efficient Supply Chain Measures Solve Production Limitations
Closed-vial technology has aided in helping to meet the increasing demand for sterile vial fillings. However, certain limitations in this technology are restraining health providers from adopting the same.
Closed vial-fillings bring about many changes to workflow and supply chains that cannot be easily adopted by CMOs (Chief Medical Officers). Closed vials need to be held still during piercing and laser sealing. This leads to high investment costs for the installation of new equipment that supports these closed vials. Closed-vial fillings also require different validation from regulatory authorities as compared sterile filling. Thus, manufacturers must take into account efficacy, quality, and patient safety to develop efficacious closed vials.
Another challenge that manufacturers face is the delamination of glass in vials. Manufacturers use borosilicate glass compositions to support sterile injectables due to their hydrolytic performance. However, the delamination of borosilicate glass leads to visible flakes and glass lamellae, which has led to many product recalls by companies. This is why manufacturers are introducing boron-free glass to develop vials. For instance, Corning – an American pharmaceutical technology company, announced the launch of Valor® Glass, which eliminates delamination with its aluminosilicate formulation in vials.
Read TMR Research Methodology at: https://www.transparencymarketresearch.com/methodology.html
Read Our Latest Press Release: