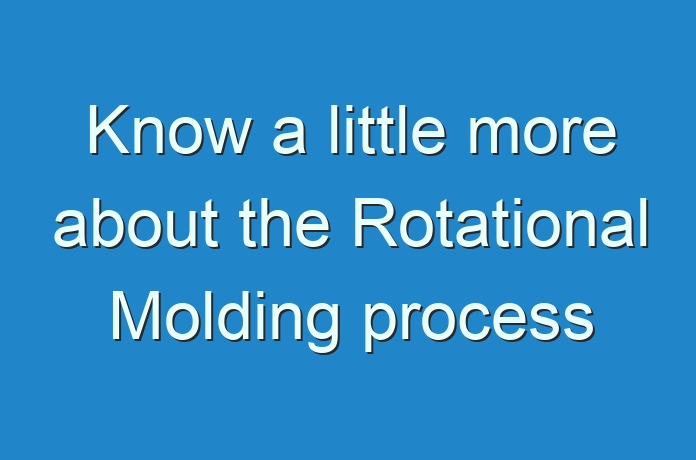
One of the most widely used materials worldwide is plastic; this is part of most daily utensils. Different processes are needed to transform this popular material into what reaches the homes.
One of the most popular processes is Rotational Molding, one of the oldest plastic treatment processes. This is carried out under thermo fusions to create infinite pieces under different molds.
The Rotomolding Process is one of the preferred processes for the production of plastic because it allows the creation of hollow parts. That is to say, when it enters the rotational molds, the plastic perfectly recreates this type of part without any problem.
That is why operators in the plastics industries prefer these processes par excellence since the adaptation is superior. They do not have any limitation of form when carrying out this type of process.
The process involves pouring the liquid plastic or powder into a mold to rotate it in 2 biaxial axes at the same time as heating. So the plastic enters all surfaces and takes the shape of the mold without problems.
Creating new pieces with hollow shapes that serve to help at home or in some industry since this process is used to create everything from household utensils to construction pieces.
So every time you see a plastic tie ring or washer, you will know that Rotomolding created these. Since the only way to give it a hollow finish is this so that you can keep the perfect standard measurements.
These molds are manufactured precisely to create standard measurements that serve only for a fusion. This is the case of hardware parts since they need common measures to be coupled to other components.
Rotational Molding and hardware
One of the most common uses of the CustomRotomolding es is to make plastic parts for hardware use. That is to say, all those unions and pieces that are needed to install the pipes and are of exact measurements
They come made by this type of process that allows you to create a hollow and smooth surface that is ideal for bonding together. Some of them need coiling that can either come with the mold or be created by another process.
Everything will depend on the utility given to the piece and its function within the complex. As long as the plastic’s strength and durability are needed, the Rotational Molding will be ideal for the manufacture of parts.
Since this technique, the properties of the plastic are not completely lost, it is one of the advantages. It preserves many of the properties that this material contains intact because the treatment is not as invasive as others.
This leads to the pieces having greater durability over time and, therefore, better market conditions. So if you need a part that is of quality and durability, these parts are the ones.
With the passing of the years, this process becomes more sophisticated, incorporating the best technologies to improve the details. This is how the best furnaces for thermo fusion enter and the parts that allow the entire manufacturing process to be controlled. This is a process that must be carried out with well-measured accuracy and precision. Since the slightest error damages the entire process and therefore, the material that is being used is lost.
For this reason, true experts in the field are used to certify the temperatures throughout the process. So that the pieces created are of the best possible quality.