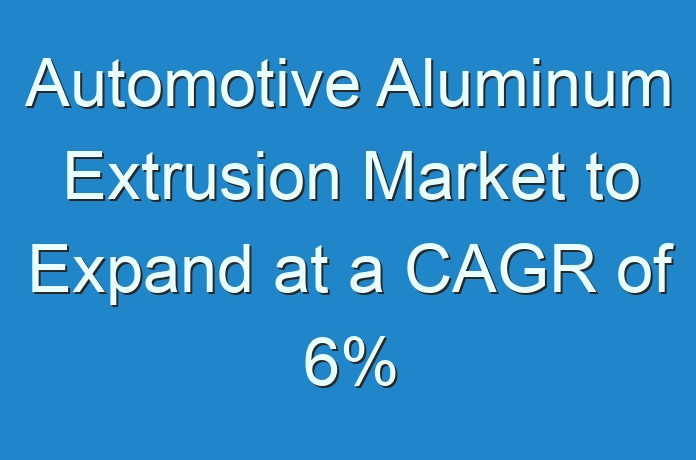
Public Transportation Sector Fuels Demand for Extruded Structures amidst COVID-19 Era
In the first half of 2024, companies in the automotive aluminum extrusion market experienced a dip in sales volume and sales revenue due to factory shutdowns and trade restrictions owing to the COVID-19 (coronavirus) pandemic. Companies are anticipating an upward trend in market growth by the end of 2024, as the pandemic subsides in Europe, the U.S., India, and Russia. Currently, manufacturers in the automotive aluminum extrusion market have resumed full operation in countries with limited number of COVID-19 cases.
Manufacturers are adopting contingency plans to address future uncertainty in businesses. Apart from vehicles, manufacturers are catering to the needs of end customers in the public transportation sector. They are maintaining business continuity plans with customers who are a part of essential sectors in the automotive industry.
Request a sample to get extensive insights into the Automotive Aluminum Extrusion Market
Electric Vehicles Set Pace for New Mobility Standards
Aluminum is gaining popularity as the fastest growing automotive material. Electric vehicles (EVs) are driving the automotive aluminum extrusion market. The growing use of aluminum in chassis applications, vehicle closure parts, and body-in-white parts are bolstering market growth. As such, automakers are adapting to new mobility standards, and are bullish on the growth of aluminum in the EV sector.
Analysts at the Transparency Market Research (TMR) are anticipating Y-O-Y growth for the automotive aluminum extrusion market, as EVs are becoming readily available for customers. Moreover, aluminum extruded structures help to offset the battery weight and lead to fuel savings. Improved vehicle performance is the key advantage of automotive aluminum extruded components.
New Aluminum Alloys with Thermal Deformation Suit Lightweight Applications
The automotive aluminum extrusion market is anticipated to grow at a favorable CAGR of 6% throughout the assessment period. This can be attributed to manufacturers being keen on using aluminum alloys in lightweight applications. However, the connection mode is limited in the case of aluminum alloys, which leads to problems in riveting and welding, resulting in poor static performance. Hence, companies in the automotive aluminum extrusion market should collaborate with researchers to develop new aluminum alloys using cost-efficient methods such as thermal deformation, micro alloying, and heat treatment.
Manufacturers are tapping value-grab opportunities in North America. For instance, Norsk Hydro ASA— a Norwegian aluminum and renewable energy company, is investing in output capacities for approx. 23 locations in North America with its enormous competency in design and technical support. Manufacturers are adopting latest technologies in metallurgy and application engineering to gain market recognition.
To understand how our report can bring difference to your business strategy, Ask for a brochure
Collaboration with Universities Helps to Narrow Gap in R&D and Production
Groundbreaking innovations in extrusion equipment are contributing toward the growth of the automotive aluminum extrusion market. For instance, manufacturers should take cues from the Constellium University Technology Center at Brunel University London to develop one-of-its-kind extrusion equipment, which deploys rapid prototyping of automotive components. Automakers should use industry-standard extrusion equipment to significantly reduce development times while manufacturing components using advance aluminum alloys.
Companies in the automotive aluminum extrusion market need to increase R&D muscle to innovate in new alloy processing technologies meant for lightweight applications. They are setting their collaboration wheels in motion with R&D centers at leading universities to develop extruded components as per the automaker’s specifications. Rapid prototyping is the key to reduce development time of vehicles. R&D centers are conducting simulation and precision testing for crash, towing, and assembly processes.