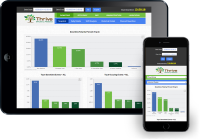
One minute, your production lines are operating exactly as they should be and everything is going smoothly. Then, disaster strikes – a key piece of equipment is offline and you now have to figure out why. You and your maintenance crews head out onto the factory floor and diagnose the issue – a process that takes roughly an hour. You realize that the issue is going to cost about $1,000 to fix before everything is back up and running again.
You order the parts you need, you perform the work you need, and that machine finally goes online. So, in that scenario the cost of this one downtime incident was about $1,000, right?
Not necessarily.
One of the reasons that downtime software can be so devastating in apparel and textiles manufacturing in particular is because there are so many more costs involved than just the obvious. Those hidden costs add up in more ways than one – all of which are more than worth a closer look.
Tracking the (Hidden) Costs of Downtime
For the sake of discussion, let’s focus on those unplanned downtime incidents. Planned downtimes are a different animal altogether because they’re typically not only scheduled, but budgeted for as well. This can include but is certainly not limited to things like scheduled maintenance, product changeover and more.
Unplanned downtime are those incidents that happen totally without warning. They last indefinitely and they can create some pretty significant backups in your production lines along the way.
From that perspective, the major hidden cost of an unplanned downtime event has to do with productivity. Every minute that machine is offline is a minute that you’re not taking full advantage of the maximized hours in a work day. This can’t help but reduce your ability to actually generate venue from what you’re producing, too.
Then, you have to think about both your tangible and intangible costs. The tangible costs are those physical problems associated with downtime in textiles and apparel manufacturing. In addition to lost production capability (which again translates to lost potential profit), you also have to deal with lost capacity. This could make it difficult to capitalize on a sudden increase in demand in the future.
You also need to consider your direct labor costs – your production levels are going down during a downtime event, but your labor costs are staying the same.
One also needs to think about the stress that an unplanned downtime event can have on your employees – a ripple effect that doesn’t necessarily go away as soon as that machine goes back online. Downtime delays them from being able to finish their work and hit their goals for the day, too, and the stress from this happening far too often can absolutely impact engagement in a negative way.
All of this is why it’s so critical to gain as much understanding over your own downtime incidents as possible – something that solutions like Thrive MES are designed to allow you to do. If you have actionable information about the most common types of downtime events you experience and what is really causing them, you’re in a better position to stop them from getting bigger or even stop them from happening again in the future.
At the very least, you’re not dealing with all of these wild and unpredictable hidden costs during a time when you can’t really afford to do so – which is ultimately the most important benefit of all.
If you’d like to find out more information about the hidden costs of downtime in apparel and textiles manufacturing, or if you’d just like to talk to someone about your own situation in a bit more detail, please don’t delay – contact Thrive today.