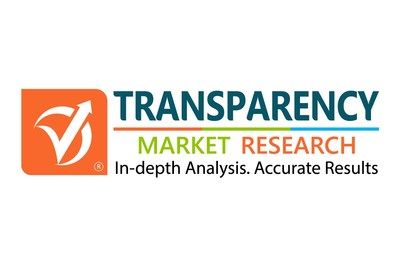
Flexibility has become the key focal point for manufacturers in the case packers market. There is growing demand for flexibility in case packaging amongst stakeholders in the F&B value chain. Top innovations such as machine-to-package flexibility, minimized downtime, and simplified changeovers are some of the major drivers for the case packers market.
Case packaging has become primarily important for beverage manufacturers. As such, the food and beverage domain accounts for the highest production amongst all end uses in the case packers market, with an estimated output of ~11,500 units by 2027. This is well justified, since manufacturers are increasing efforts to develop advanced automatic case packers that provide retail-ready packaging designs.
There is growing demand for innovative packaging equipment that is easy-to-use and which can manage quick changeovers. Companies in the landscape are increasing efforts to fulfill the demand for case packers that can run more than one packaging design. The trend of multiple package formats is benefitting the production of shelf-ready packages.
As consumers are becoming increasingly aware about sustainable packaging solutions, equipment companies in the case packers market are streamlining their production to meet consumer demand. They are regularizing equipment manufacturing processes to innovate new packaging designs. Since case packaging plays a crucial role in secondary packaging, retailers in the value chain are demanding that companies follow the same guidelines.
Request PDF Sample For More Information@
https://www.transparencymarketresearch.com/sample/sample.php?flag=S&rep_id=17252
Sustainable packaging solutions help companies comply with strict regulatory norms that lead to reduced material usage. Companies are increasing their production capabilities to manufacture recyclable materials that further lead to reduced environmental impact. Leading hypermarkets and supermarkets are achieving sustainability goals with the adoption of fully-recyclable retail ready packaging.
Sustainability is creating a new trend in flexible packaging. Companies in the market are developing new versions of case packers that are optimized for flexible products, such as pouches and rigid containers (bottles). The introduction of new packaging designs has led to the development of novel recyclable corrugated materials.
Companies Investing in Advanced Engineering to Take Lead in the Market Landscape
Equipment companies in the case packers market are increasing R&D to onboard the best engineering talent to drive innovation in case packaging and wrapping equipment. They are focusing on developing state-of-the-art case packing machines that are more versatile in operation and require minimum maintenance. Companies in the case packers market are increasing efforts to equip case packers with seamless pick-and-pack patterns at high speeds. This phenomenon eliminates the need for additional parts such as buckets, collation chains, fixed guides, and the like.
The trend of less equipment parts serves as a cost-efficient solution for end users in the packaging and processing landscape, as minimum parts leads to lesser maintenance costs. This trend is directly correlated with less capital investment for the production of equipment. Also, 3D printed replacement parts are a new driver in the landscape.
Read Latest Press Release@ https://www.prnewswire.com/news-releases/chemical-sensors-market—adoption-of-nanosensors-in-myriad-applications-to-spur-demand-says-tmr-300872610.html
Innovations in Robotic Case Packers Ignite OEM Opportunities in F&B Space
Investments by packaging and processing stakeholders in robotic case packers have created incremental opportunities for OEMs. As such, the production of robotic case packers is estimated to skyrocket to a record of ~15,000 units by the end of 2027 in the case packers market. This is why, OEMs, in the case packers space, are introducing new innovations in equipment to find creative ways that address the new demands of end users.
Apart from the automotive sector, there is growing demand for robotic case packers in the F&B and personal care sectors in America. However, stringent regulations govern the deployment of robotic case packers in the F&B space. Thus, companies in the case packers market need to address these norms that limit the use of robots in palletizing applications. As such, they are strategizing by developing hygiene robots with wash-down capabilities to complement robotic case packers. These hygiene robots fulfill the need for sanitary solutions in wash-down environments of the F&B packaging landscape.