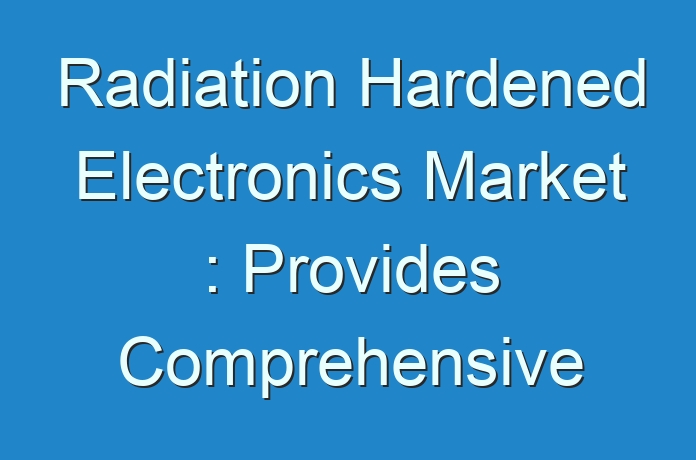
An act of producing the electronic systems or components resistant to malfunction or damage done by ionizing radiation (electromagnetic radiation and particle radiation of high energy) is called as radiation hardening. These radiations are encountered in high-altitude flight and outer space, around particle accelerators and nuclear reactors, or during nuclear wars and nuclear accidents. Most of the electronic components are prone to damage by these radiations. However radiation hardened electronic components are placed on the non-hardened components with some manufacturing and design variations reducing the vulnerability to radiation damage. Extensive testing and development is required in producing a microelectronic chip which is radiation tolerant, radiation hardened electronic chips lag behind in new developments. TID (Total Ionizing Dose), EDLRS (Enhanced Low Dose Rate Effects), single event effects (SEE, SEB, SET, & SEL), and proton & neutron displacement charge are some of the tests used typically for radiation-hardened products testing. Cosmic rays, solar particle events, Van Allen radiation belts, secondary particles, particle accelerators, chip packaging materials are some of the major radiation damage sources. There are two types of radiation hardening techniques logical hardening and physical hardening. Techniques included under physical hardening are production of electronic components by insulating substrates like silicon on sapphire and silicon on insulator. Bipolar ICs (Integrated Circuits), magneto resistive RAM (Radom Access Memory), capacitor based dynamic RAM (Random Access Memory) and shielding packages are radiation hardened. Logical radiation hardening techniques are redundant elements, hardened latches, parity checking, and watchdog timer for reducing radiation impact on electronic components.
Request for a sample:
https://www.transparencymarketresearch.com/sample/sample.php?flag=S&rep_id=7469
The major factor driving the radiation hardened electronics market is rising demand for power management devices. Another factor augmenting the market for radiation hardened electronics market is rising demand for diodes, transistors, and MOSFETs in various defense and space applications. More technological advancements is leading to focus on integration of radiation hardened electronics chip into various devices. Another major driver for the market is the increase in the number of the space missions. One of the driver for the radiation hardened electronics market is rise in demand for communication satellites. Growing ISR (Intelligence, Surveillance, and Reconnaissance) operations, multicore processor technology and FPGA advancements will drive the radiation hardening electronics market in future. However the major challenge for the market is high cost involved in developing and testing the radiation hardened electronic devices. But rise in investments in R&D (research and development) of semiconductors and electronics will minimize the impact of this challenge. Another challenge being faced by the radiation hardened electronics market are the emerging of small satellites (SmallSats) with small life cycle. This small satellites market is called Space 2.0.
PreBook Now:
https://www.transparencymarketresearch.com/checkout.php?rep_id=7469<ype=S
The radiation hardened electronics component market can be segmented based on components (power management, ASIC, logic, memory, FPGA), manufacturing technique (RHBD radiation hardening by design, RHBP Radiation hardening by process), application (space, aerospace & defense, nuclear power plant), geography (North America, Europe, Asia-Pacific, rest of the world).
Read Latest News Publication: