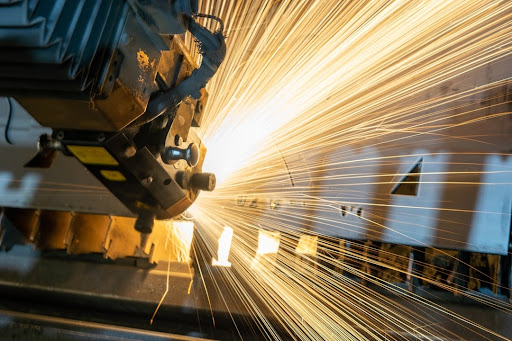
As businesses evolve with digital transformation, organizations are left looking to curb their downtime while assuring safety and transparency in real-time issues. That’s where predictive maintenance comes into play.
Also known as condition-based maintenance, this process monitors performance and equipment conditions during regular operations to reduce the chance of breakdown on a supply chain.
The ultimate goal is to predict equipment failures based on specific parameters and factors. Let’s take a closer look at some of the skill sets that a maintenance team may need to execute this ability better.
Infrared Thermography
Having the right maintenance professionals and programs in place starts with having the right predictive maintenance software. For example, infrared thermography is widely used in predictive or preventive maintenance.
With infrared cameras, maintenance personnel can spot above-average temperatures in equipment. This encompasses reactive maintenance by spotting malfunctioning circuits that tend to heat up when they’re worn out. Infrared inspections can find these hot spots in real-time to repair equipment.
This reduces the chance of more significant issues and greater ease of use across a wide variety of machinery and infrastructure projects.
Infrared thermography also allows business owners to take a maintenance approach based on the equipment they include in a program’s initial implementation. Predictive maintenance technology evaluates any pre-existing protocols and establishes the need for repair sooner.
Acoustic Monitoring
Acoustic monitoring helps detect issues with equipment based on sounds like gas emission, liquid, or vacuum leaks. Ultrasonic technology has far more applications in maintenance activities, as it’s a far more reliable approach to technology for machinery.
These technologies supplement a technician’s best tool: their ears. Ultrasonic technology supplements regular listening to better detect why a gearbox sounds off or where a possible leak might be stemming from these critical assets.
By recognizing these audible problems with production equipment, a predictive maintenance program can avoid any issues in the long run with equipment faults.
This avoids any downtime or excessive maintenance costs brought on by lost production and energy. This can be done with regular evaluation and appraisal of equipment.
Vibration Analysis
Vibration analysis is used when dealing with high-speed rotating equipment as part of a manufacturing process. Technicians use handheld devices and real-time sensors to monitor functions.
When a machine performs at its best, those pieces of equipment emit a specific rhythm of vibration. As a result, a new pattern emerges in the vibration throughout equipment lifespan that helps analysts detect components that could be wearing down over time.
Vibration analysis can detect misalignment, unbalanced elements, loose mechanical components, and motor issues. Technicians need to be well-trained for the job as predicting vibration analysis is complicated.
This is crucial to a cost-effective maintenance strategy to avoid downtime or unnecessary costs for earlier preventable issues. Early alerts can make sure that uptime remains proficient throughout the supply chain.
Oil Analysis
Oil analysis is an effective tool in predictive maintenance. By checking oil conditions, technicians can establish the presence of contaminants at any point of failure throughout a supply chain. First, oil analysis determines viscosity, water, and particle counts.
From there, an acid or base number is established as part of a predictive maintenance system. The main benefit of oil analysis is that its initial test results serve as a baseline for any new machinery and maintenance.
This requires true knowledge of the inner workings of the mechanisms and the forthcoming products. For this maintenance process to succeed, you need a technician who can operate under proper maintenance schedules to ensure that systems and operations work seamlessly.
Predictive maintenance can be the best way to protect equipment, workers, and the bottom line alike.