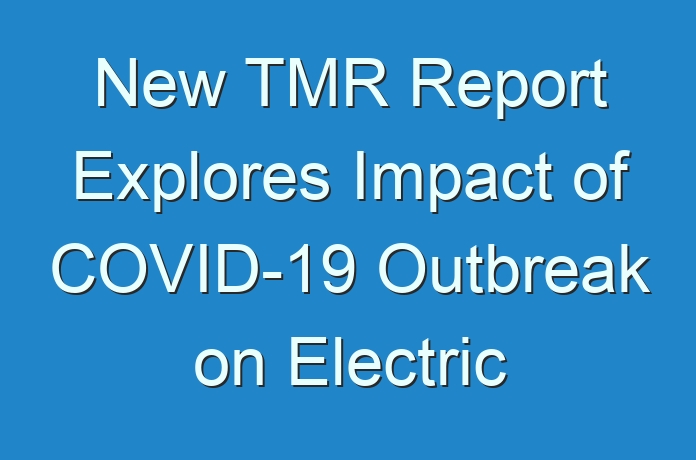
Electric Discharge Machine – Ideal Substitute for Traditional Machining Techniques
The manufacturing sector worldwide is booming at a rapid pace. With the growing emphasis on precision and accuracy, conventional machining techniques are gradually being replaced by non-conventional machining processes, thereby driving the growth of the global electric discharge machine market. Among all the non-conventional machining processes deployed across the manufacturing sector, electric discharge machining has emerged as one of the most efficient techniques, which caters to the evolving requirement of the manufacturing sector. Electric discharge machines are extensively used across a broad range of industry verticals, including automotive, aerospace & defense, manufacturing, healthcare, and electronics.
As electric discharge machines have time and again assisted manufacturers to achieve the desired accuracy levels, its adoption is growing at a steady rate. The electric discharge machine market, which was valued at ~US$ 4.5 Bn in 2018 and is poised to attain a value of ~US$ 6.1 Bn by the end of 2027. The growth is expected to be primarily driven by advancement in technology, escalating demand from pharmaceutical device manufacturers, and inefficient conventional techniques such as grinding, milling, and polishing.
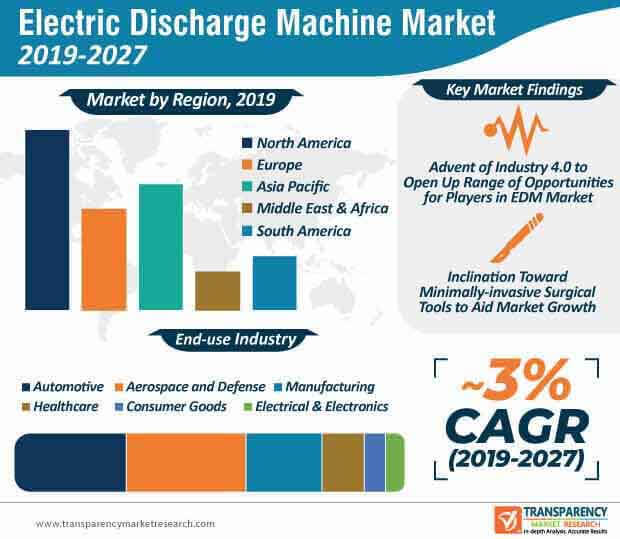
Request a sample to get extensive insights into the Electric Discharge Machine Market
Adoption of Cost-effective Wire Electric Discharge Machines to Gain Momentum
Among the different types of electric discharge machines, wire cutting electric discharge machines have gained significant popularity over the past couple of decades. Electric discharge machines were typically developed to overcome the shortcomings put forward by traditional electric discharge machines. These machines entered the electric discharge machine market in the late 1960s and were predominantly used to manufacture hardened steel and dies. However, at present, these machines are widely used to manufacture fixtures & gauges, extrusion tools, medicals parts, etc. Furthermore, wire cutting electric discharge machines are extensively used to extract complex and irregular shapes in various hard-to-machine conductive materials in nuclear, aviation, and automotive applications.
To understand how our report can bring difference to your business strategy, Ask for a brochure
Within the electric discharge machine market landscape, wire cutting electric discharge machines are increasingly being used to machine multiple micro-scale parts in sintered materials such as metals, ceramic, silicon, and alloys. Owing to these benefits, the demand for these machines continues to increase at a steady pace. In terms of value, the wire cutting electric discharge machines segment is projected to account for over 80% of the market share in 2027, and attain a value of ~US$ 4.9 Bn by the end of the forecast period (2019-2027). At present, players operating in the global electric discharge machine market are focusing on improving the cutting speed, accuracy, and reducing the overall machining costs.
Focus on Achieving Green Manufacturing with Electric Discharge Machines
Cutting-edge discharge machines have gradually replaced traditional machining techniques, owing to their commendable hard material processing capabilities and accuracy. However, with looming concerns over environmental degradation, the industrial sector is compelled to lean toward green manufacturing processes. The application of dielectric fluid used in electric discharge machining poses a threat to the environment – a challenge that requires a swift and timely response from key participants operating in the current electric discharge machine market landscape.
Research and development activities are paving the way for greener machining solutions, including semi-dry EDM, dry EDM, and EDM in water – replacing the conventional oil EDM process. In their quest toward green manufacturing, market players are focusing on refining the existing EDM process by using novel techniques, including dry EDM. Furthermore, as these techniques do not use mineral oil-based liquid dielectric, oil-based dielectric wastes that cause significant harm to the environment are absent. Thus, dry EDM is gradually garnering the reputation of being an eco-friendly machining process. Additionally, by adopting this technique, market players aim to improve the efficiency of their processes and minimize operating costs.
Market Players Develop Products in Accord with Requirements of Industry 4.0
With the introduction of Industry 4.0, cutting-edge technologies, including the Internet of Things (IoT), cyber-physical systems, and cloud computing, among others have penetrated the modern-day industrial landscape. Key participants in the global electric discharge machine market are currently on course toward the development of new products that are in tune with Industry 4.0. Companies are focusing on expanding their product portfolio and incorporating novel technologies to stay relevant in the current market. For instance, GF Machining Solutions launched an ultramodern wire-cutting EDM machine that aims to enhance productivity, speed, accuracy, and quality.