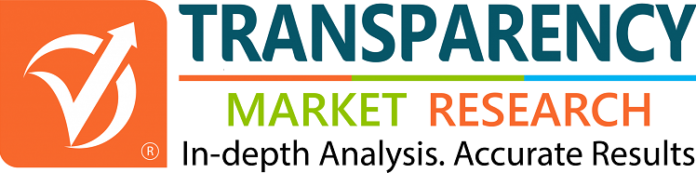
Integrated circuit packaging is a last process of semiconductor device manufacturing. In this process, a small portion of the material used to make the semiconductor device is wrapped in a supplementary case. This is mainly done for avoiding physical damage as well as corrosion activities that might negatively affect the semiconductor device. The supplementary case, which is also called package, is utilized to provide a medium for passage of electrical contact. This electrical contact further forms a bridge between semiconductor devices and their respective circuit boards.
Ceramic IC packages, as the name suggests, are manufactured from ceramic materials. Depending on material type, quality, and other factors, a plethora of IC packages can be made using ceramic. These packages can provide a completely sealed environment, so that the packed devices are not affected by being in contact with air, thus avoiding negative corrosion effects. The package can also be manufactured in small sizes, even if they are required to provide numerous electrical connections.
Request for a sample:
https://www.transparencymarketresearch.com/sample/sample.php?flag=S&rep_id=19154
Ceramic IC packages are mainly manufactured by using two methods: dry pressing and multilayer structure. The first method involves using a mixture of ceramic and binders. This mixture is further molded by employing a dry pressing process, thus earning the name. This dry pressing process finalizes the shape of the products, which is further followed by the components being sintered into a finished framework. In this way, the ceramic IC packages assume a form similar to a sandwich, wherein a frame made from lead metal is placed between two ceramic components, by using the dry pressing method. These packages are less costly as compared to the ones manufactured through multilayer process. However they also have limitations associated with less electrical features due to a simple construction.
In contrast, the multilayer IC packages use ceramics that have not been subjected to heat, and combining with screen-printed tungsten, to provide a metallic appearance. The entire set is then exposes to high temperature and pressure.
Integrated circuit packaging is final stage of the semiconductor device fabrication, in which a tiny block of the semiconductor material is encapsulated in the supporting case that is used to prevent any physical damage or corrosion. The case which is called as “package” is used to support the electrical contact which connects the device to the circuit board. Ceramic IC packages are the package that mainly use ceramic materials. A wide variety of IC package types use ceramic materials. One of the main properties of ceramic IC packages is that they can be sealed hermetically and even with large number of electrical connections they can be manufactured in small sizes. There are two methods used for the fabrication of ceramic IC packages. One method uses the mixture of ceramic and binders which is then molded by dry pressing process into a shape and finally sintered into a finished component. Thus the ceramic IC Package is formed by sandwich of a metal lead frame between dry pressed ceramic components. These ceramic IC packages have less cost but the simple construction limits their electrical features. Another approach is using multilayer structure. This method involves unfired (green state) ceramics metallized with screen-printed tungsten pattern. These are fired at high temperature under pressure.
The major driver for the ceramic IC packages market is the simple and easy manufacturing as compared to the plastic IC packages. Another major driver for the ceramic IC packages market is the increasing demand to meet the stringent requirements for reliability. One of the key factors in the growth of the ceramic IC packages market is the increasing application of ceramic IC packages in the commercial defence and aerospace industry. One of the serious issues like inability to handle temperature cycles with the plastic IC packages in recent past has led to the growth of the ceramic IC packages market. Absorption of moisture by plastic IC packages makes them inappropriate for usage in different applications which has further augmented the ceramic IC packages market. Maximum use of high temperature co-fired ceramic packages in different applications like tablets, computers, smartphones, automotives and spaceships is driving the ceramic IC packages market. The major challenge faced by the ceramic IC packages market is the high cost of manufacturing. Another challenge faced by the ceramic IC packages market is the heavy weight of ceramic IC packages as compared to the plastic IC packages.
Ask for brochure:
https://www.transparencymarketresearch.com/sample/sample.php?flag=B&rep_id=19154
The ceramic IC packages market can be segmented based on the application (Automotives, Communication, Industrial Equipment, Defence, Healthcare, and Aerospace), based on Package Type (DIP (Dual Inline Packages), SIP (Single Inline Packages), and PGA (Pin Grid Arrays)), and based on geography (North America, Europe, Asia Pacific, Middle East & Africa, and Latin America).
Automotives accounts for the largest ceramic IC packages market as automobiles require highly reliable IC packages. Defence and Aerospace accounts for the second largest market as this sector also requires highly reliable IC packages. North America is the largest market for the ceramic IC Packages owing to its high application in defence and aerospace. Europe is the second largest market for ceramic IC packages owing to the biggest manufacturing market for automobiles. Asia Pacific is the largest growing market for the ceramic IC packages due increased measures by government in defence and aerospace in these regions.
Some of the key players include Amkor technology (U.S.), Quik-Pak (U.S.), NGK (Japan), Alent Plc. (U.K.), Hitachi Chemical Co. Ltd. (Japan), Kyocera Chemical Co. Ltd.(Japan), LG Chemical Ltd. (South Korea), Sumitomo Chemical Co. Ltd. (Japan), Basf Se (Germany) , Mitsui High-Tec Inc. (Japan), Henkel Ag & Company (Germany), Toray Industries Corporation (Japan), Tanaka Holdings Co. Ltd. (Japan).
Read our latest press release