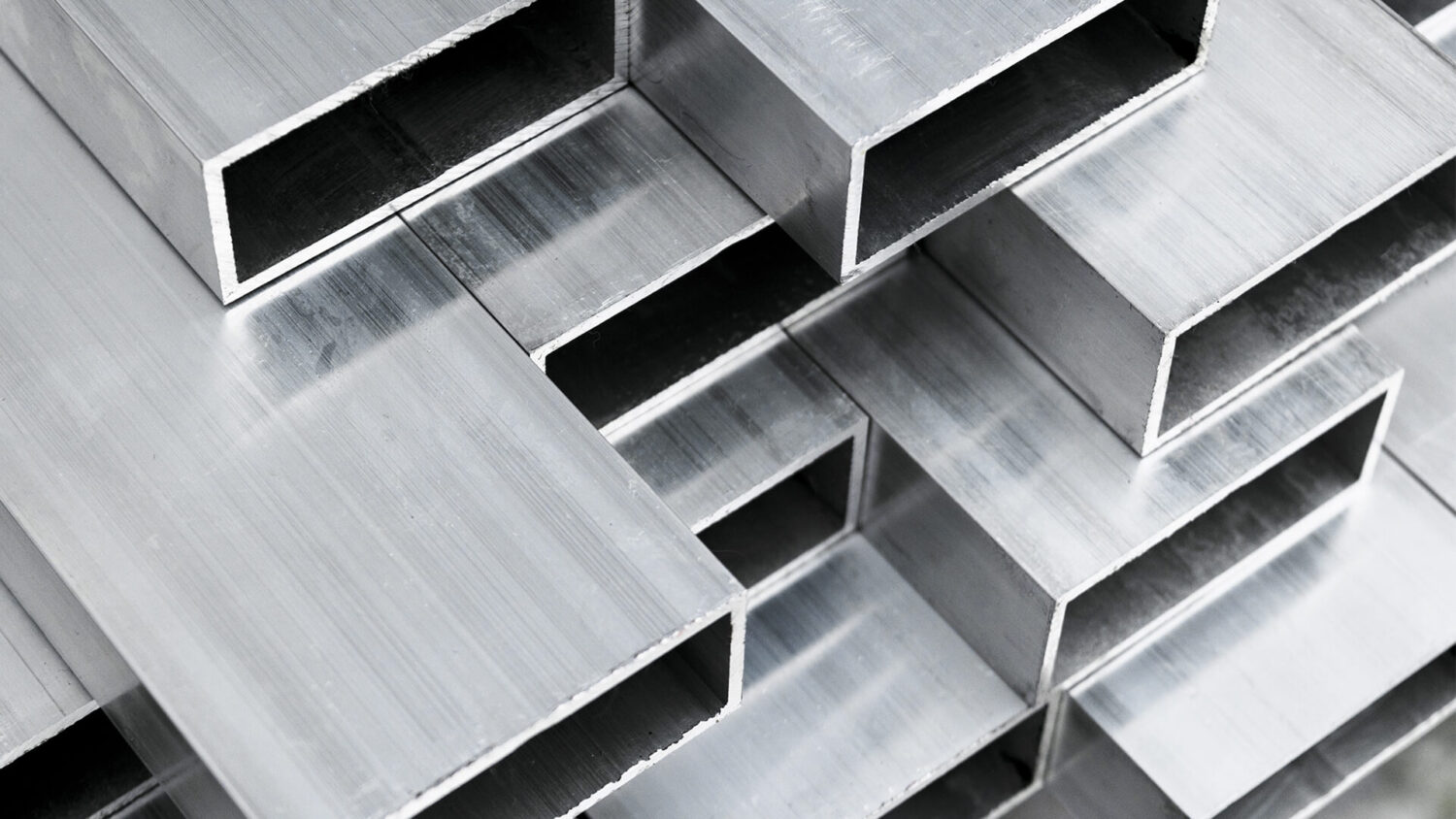
Aluminum extrusions are widely used in many industries today and have the potential to be even more useful. With their ability to be easily manipulated and formed into almost any shape, aluminum extrusions can provide an incredibly versatile solution for many projects.
However, working with aluminum extrusions can present certain challenges that need to be addressed in order for these solutions to truly reach their potential.
In this article, we will discuss some essential tips for successfully working with aluminum extrusions so you can unlock the full capability of these materials.
Preparing Aluminum for Processing
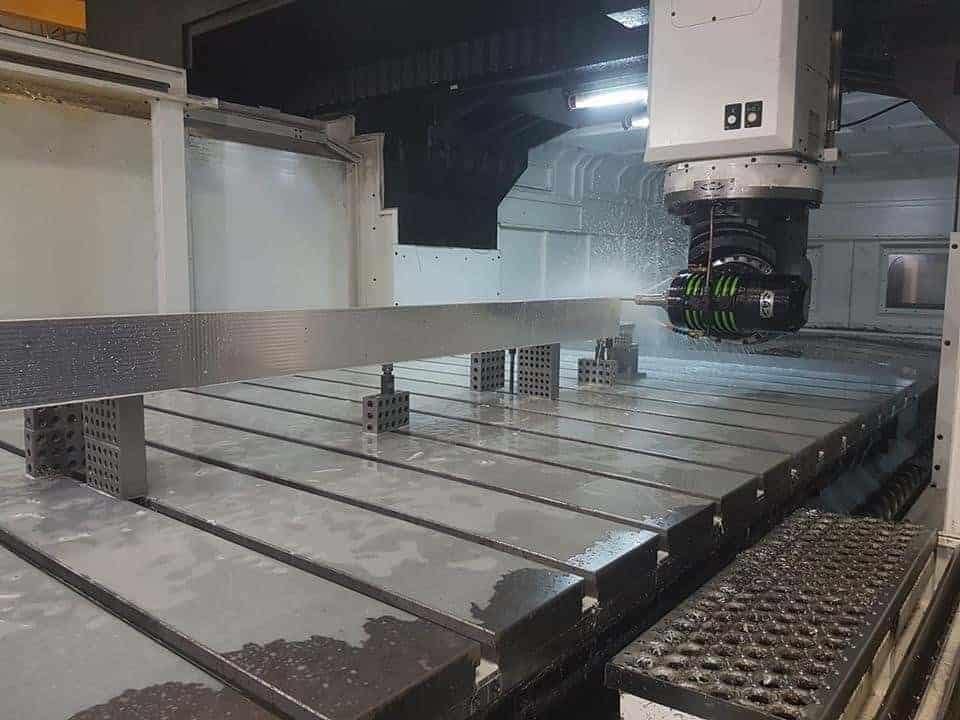
Preparing aluminum for processing is a necessary step in unlocking the potential of aluminum extrusions. Proper preparation ensures that the finished product meets all quality and safety requirements, while minimizing costly manufacturing delays.
To begin, its important to select an alloy appropriate for your application – from 6061-T6 to 2024-T3 — ensuring excellent strength and corrosion resistance. Next, prepping the metal by cutting and sawing to specific dimensions requires precise measurements and sharp tools; mistakes can lead to poor accuracy or even wastefulness due to rework or scrapping.
Finally, removing any burrs or imperfections produced during cutting will result in a smoother finish on your final product. Taking these steps before extrusion will help you get the most out of this versatile material!
Selecting the Right Tools for Working with Extrusions

Selecting the right tools for working with aluminum extrusions is critical to unlocking their potential. Having the correct equipment and materials can save time, reduce waste, and ensure optimal results.
When considering which tools are best suited to your project, it’s important to consider factors such as the type of extrusion material youre using, size of shapes needed, and any other specific requirements in order to select the most suitable solution.
Some common options include hand-held saws or metal cutters for smaller projects; hydraulic shears or cold saws for larger pieces; CNC machines when accuracy is essential; waterjet cutting services for intricate shapes; or heat knives if an extremely clean finish is desired. Each tool has its own strengths and weaknesses that must be taken into account in relation to each individual project before making a final selection.
By carefully assessing needs up front and choosing the right tools accordingly, you can make sure that your aluminum extrusion project runs smoothly from start to finish!
Conclusion

Aluminum extrusions are a versatile and cost-effective material for a variety of projects. While they offer many advantages, it’s important to understand the basics of working with them in order to maximize their potential.
By following these essential tips from an experienced aluminum extrusion manufacturer, you can unlock the full potential of this excellent material and create products that will stand up to the test of time.