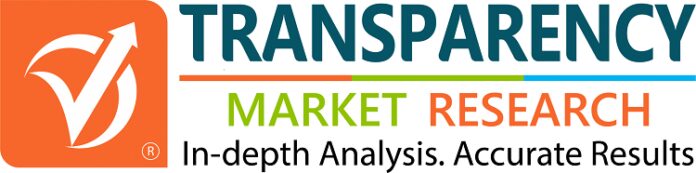
Transparency Market Research delivers key insights on the global slewing drives market. In terms of revenue, the global slewing drives market is estimated to expand at a CAGR of ~ 5% during the forecast period, owing to numerous factors, regarding which, TMR offers thorough insights and forecasts in the slewing drives market report.
Slewing drives are gearboxes that have two to four planetary stages. These drives comprise a planetary gear unit that is robust, compact, and versatile. These gear units are made from high alloy steel. The unit is equipped with a hydraulic fail safe wet type multi-disc and electromagnetic brake. Slewing drives are optimized for best possible tooth flank and root load capacity, and minimum sliding speeds. Their design optimizes torque performance capacity and radial load capacity, while bending stresses are kept within limits to give the perfect meshing between the pinion and gear. Slew drive rings consist of a slew bearing worm shaft, housing, shaft bearings, and a motor with a hollow bore. The motor drives the motor shaft, which, in turn, drives the outer ring of slew bearing and causes it to rotate.
In this market report, TMR estimates that the wind turbines & solar tracker system segment will outpace other applications by the end of 2027, in the slewing drives market. Rise in construction is the primary reason for the growth in the demand for slewing drives across the globe. Increase in government initiatives are expected to drive the growth of the slewing drives market during the period of 2019 to 2027. All these factors are leading to the increasing demand for slewing drives. However, the high cost of equipment and high maintenance cost are expected to hamper the market during the forecast period. Slewing drives need regular maintenance and lubrication, and if this is not done, the remanufacturing cost of the drives becomes steep.
Request Sample For More Information@
https://www.transparencymarketresearch.com/sample/sample.php?flag=S&rep_id=59133
The Step toward High-Precision & Non-Standard Customization
Stakeholders in the slewing drives market saw a marked rise in new OEM customers, complementing business margins, and driving investments in new production lines and capacity expansions. According to TMR’s study, ~800 thousand units of slewing drives were sold in 2018, and the market is estimated to record ~ 4% CAGR through to 2027.
From the perspective of demand-side dynamics, as the construction machinery gets caught up in the new maintenance cycle abreast surging infrastructure development activities, there is huge requirement for load transmission components such as slewing drives. Additionally, structural adjustments in the manufacturing sector have led to a rise in new facilities, including automation and energy, which has driven the demand for high-quality slewing drives with emphasis on high-precision and non-standard customization.
Versatility in performance is another key aspect that has been gaining the attention of slewing drive manufacturers, devoid of the component’s mechanism – vertical or horizontal. Slewing drives that offer a wide spectrum of torque have been introduced by established manufacturers to suit the various performance requirements of end users. Hourglass technology used in slewing drives have also witnessed significant advancements to cope up with the low-maintenance and performance versatility needs of customers. The focus on greater strength and accuracy has led manufacturers to focus on increased tooth engagement, which has consequentially complemented offering high torque in confined spaces.
Request For Custom Research Report@
https://www.transparencymarketresearch.com/sample/sample.php?flag=CR&rep_id=59133
R&D of Anti-corrosive Materials
Key market stakeholders have strengthened their focus toward improving the reliability and lifecycle of slewing drives, and add to their application versatility. The R&D of new materials needed for slewing drives, and the R&D of auxiliary processes & materials do not meet the urging requirements for quality and performance level. This has further led manufacturers to emphasize more stringent internal standards that enable improved geometry, increased depth of hardened layer, and enhanced service life.