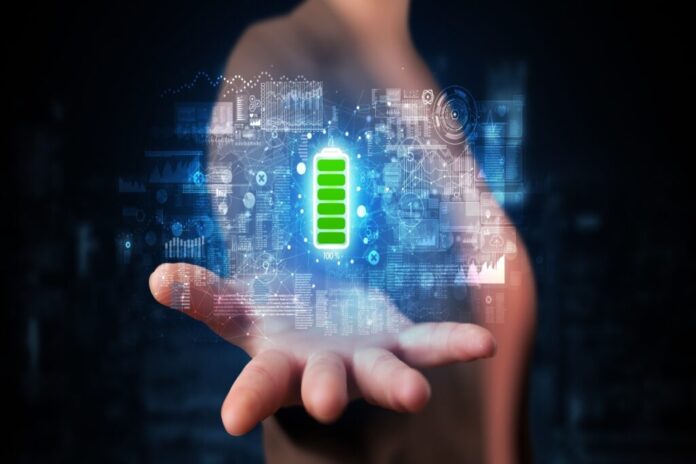
Lubrication Systems Market – Snapshot
Use of a lubrication system for a particular application depends on various factors such as frequency of lubrication, the number of lubrication points, and operating expenses incurred for manual labor. Large plants such as cement plants, steel plants, and paper mills primarily employ central or automatic lubrication systems, as the number of lubrication points in these plants is high. This reduces the time taken to lubricate several machines. It also eliminates any errors caused by manual lubrication.
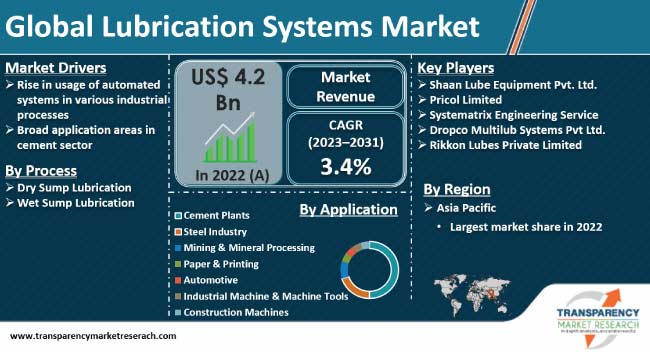
Request PDF Brochure :https://www.transparencymarketresearch.com/sample/sample.php?flag=B&rep_id=4172
Increase in demand for lubrication systems in mineral and metal processing industries
Rise in population, growth of economy, and increase in urbanization have created high demand for minerals and metals. Among metals, copper ranks third (after steel and aluminum), in terms of consumption. Currently, aluminum is the second-most used metal in the world (after steel) and the third-most available element on the earth, constituting almost 7.3% by mass. The global minerals industry has expanded significantly over the last few years. Lubrication systems are widely used in metal and mineral processing industries, as various types of equipment are subjected to extreme heavy load, high speed, high temperature, or dusty and polluted environment. Also, the positive outlook for end-user industries is expected to augment the demand for lubrication systems in the near future.
REQUEST FOR COVID19 IMPACT ANALYSIS :https://www.transparencymarketresearch.com/sample/sample.php?flag=covid19&rep_id=4172
Cement plants and steel industry key end-users of lubrication systems
In 2017, the steel industry segment constituted more than 20% share of global lubrication systems market. In the steel industry, lubrication is required at every step across the entire delivery chain. Effective lubrication is required for both upstream and downstream processes. The profitability of cement plants is directly related to equipment reliability. For reliable operations in a cement plant, frequent greasing and lubrication is required so as to prevent the entry of contaminants into bearings. Some of the systems and components in the cement industry that require lubrication are conveyors, crushers, ventilation systems, mixing beds, rotator kilns, mills, motors, and pumps. Use of a proper lubrication system is a necessity of a cement plant, as component points are exposed to extreme conditions such as high loads, high temperature, vibrations, shock loads, and contaminants.
Explore Transparency Market Research’s award-winning coverage of the global Industry:
https://www.prnewswire.com/news-releases/increasing-demand-from-end-users-to-help-potassium-formate-market-reach-valuation-of-us920-mn-by-2027-finds-tmr-301181500.html
Innovations, quality improvement, and recent advancements in lubrication systems
Companies make significant investments every year in order to improve plant design and performance. In September 2017, Graco Inc. launched the A4000 Reciprocating LubePro oil and grease pump that belongs to the LubePro series of automatic lubrication pumps. This higher-capacity, single-line parallel pump has the ability to fire hundreds of injectors at once by using Graco’s field-proven Merkur air motor. Its unique pump design leads to reduced venting times. The A4000 Reciprocating LubePro oil and grease pump has been made available in a variety of configurations to meet specific lubrication needs. With the launch of this pump, the company offers a complete portfolio of single-line parallel pumps. These pumps are manufactured in the U.S. and come with a factory-installed pressure gauge, adjustable pressure relief, and integrated low-level detection to ensure rapid and accurate lubrication of the system. In 2018, SKF launched the Lincoln mechanical grease overflow prevention system designed to mitigate hazards associated with reservoir overfilling; minimize environment-related concerns associated with this type of spill; and ensure workers’ safety. This mechanical grease overflow prevention system is suitable for mining, aggregate and industrial applications as well as for use in off-road construction equipment. In April 2018, SKF introduced the Lincoln small grease reservoir filling filter designed to minimize contaminants entering automatic lubrication systems during the filling process of smaller-sized reservoirs.
About Us:
Transparency Market Research is a global market intelligence company, providing global business information reports and services. Our exclusive blend of quantitative forecasting and trends analysis provides forward-looking insight for thousands of decision makers. Our experienced team of Analysts, Researchers, and Consultants, use proprietary data sources and various tools and techniques to gather, and analyze information.
Our data repository is continuously updated and revised by a team of research experts, so that it always reflects the latest trends and information. With a broad research and analysis capability, Transparency Market Research employs rigorous primary and secondary research techniques in developing distinctive data sets and research material for business reports.