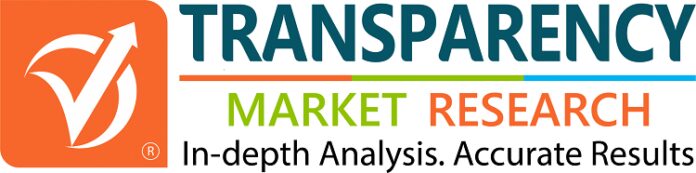
The hollow core insulator market is going through a transition stage in different regions of the world. Manufacturers produce either ceramic or composite hollow core insulators according to the preference of end-users, especially the power transmission sector in that specific region. For e.g. ceramic remains by far the preferred material for hollow core insulators in India. On the other hand, European countries are increasingly adopting composite hollow core insulation technology. However, certain parts of these countries still prefer the ceramic type. Thus, overall, the demand for hollow core insulator technology varies in different regions of the world. The global hollow core insulator market is projected to expand at a CAGR of 4.9% during the forecast period and reach US$ 4,959.2 Mn by 2026.
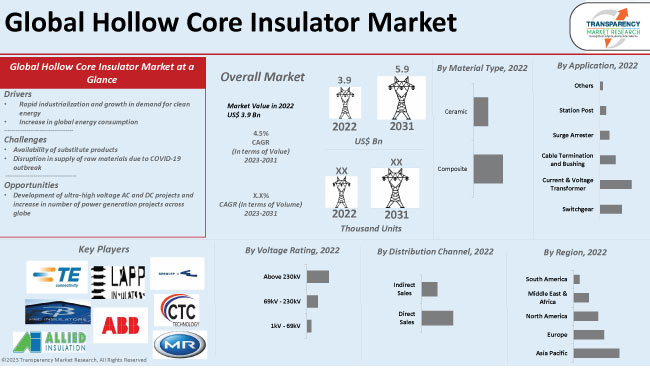
Selection of composite hollow core insulators for one to one replacement of ceramic type is expected to be the major driver facilitating the growth of the global hollow core insulators market. For higher voltage levels, ceramic is expensive and requires long production lead-times. Therefore, until recently, composite hollow core insulators were preferred at either very high voltage levels or for seismic environments only. However, currently, they are increasingly viewed as a good replacement for ceramic type at a wide range of voltage levels and applications.
Request for a sample:
https://www.transparencymarketresearch.com/sample/sample.php?flag=S&rep_id=40064
Composite insulators are made with liquid silicone rubber sheds or hydrophobic HTV. Therefore, they offer high performance under contamination with reduced creepage distances, leading to low maintenance even in the most demanding applications. Safety is another major advantage offered by composite hollow core insulators on pressurized substation equipment and personnel. Every year, several instances of disastrous equipment failures such as explosion, internal arcing, seismic stresses, or short circuit displacement of bus supports leads to material damage and injury to personnel. This is majorly due to the violent explosion of ceramic hollow core insulator with its fragments thrown at a very high speed. Since composite insulators remain mechanically intact in the event of puncture, they do not cause damage to surrounding equipment and persons in the vicinity, assuring maximum safety at the substation. Thus, important safety considerations for power utilities are expected to lead to increased preference for composite hollow core insulators, driving the overall hollow core insulators market.
However, the growing voltage levels are imposing increasing requirements on quality of composite hollow core insulators for substation equipment applications such as transformers, breakers, surge arresters, and wall bushings. Their larger size corresponds to higher manufacturing cost, which means that faulty units can lead to expensive mistakes. This is the reason the quality of various materials that are used for insulator components have to be cautiously examined at every production phase. Moreover, the threat of manufacturing errors in the form of gaps, voids, and areas of poor adhesion between the housing and the core must be reduced. This seems to be the only way to assure a reliably superior quality interface between the housing and the core. Insufficient chemical bonding at this interface, even if limited to a small area, could result in the inception of degradation process, which over a period of time could lead to failure. It is therefore crucial to gain more understanding about the performance of imperfectly bonded interfaces between the silicone rubber housing and the epoxy core, particularly when exposed to partial releases in a moist location.
Ask for brochure:
https://www.transparencymarketresearch.com/sample/sample.php?flag=B&rep_id=40064
Amongst all voltage ratings, 230 kV is expected to be largely preferred due to increasing power transmission and distribution applications across the world. Particularly, development in ultra-high voltage applications is resulting in increased installation of switchgear and current & voltage transformers amongst other applications.
Attracted by this expanding market and its underlying latent demand, several players are expanding their business through optimization of production and business processes and investment in product development to deliver innovative solutions to the industry. Some of the prominent players identified in the hollow core insulator market includes PPC Insulators Austria GmbH, Allied Insulators Group Limited, Lapp Insulators GmbH, CTC Insulator Co., Ltd., ABB Ltd, TE Connectivity Ltd, Maschinenfabrik Reinhausen GmbH, ZPE ZAPAL S.A, saver S.p.A, and CERALEP SN.
Increasing Efforts by Governments to Improve Transmission Infrastructure will Aid in Expansion of Hollow Core Insulator Market
Rising industrialization and urbanization is required to improve the market development. A portion of the other factors like expanding creation of environmentally friendly power, rising government activities to upgrade the transmission framework and developing transmission and circulation organizations will drive the hollow core insulator market.
Composite insulators are made with fluid silicone elastic sheds or hydrophobic HTV. Subsequently, they offer superior under pollution with diminished creepage distances, prompting low support even in the most requesting applications. Wellbeing is another significant benefit offered by composite hollow core insulators on compressed substation hardware and faculty. Consistently, a few cases of awful gear disappointments like blast, inside arcing, seismic burdens, or short out uprooting of transport underpins prompts material harm and injury to the workforce. This is because of the rough blast of an artistic hollow core insulator with its pieces tossed at an extremely rapid.
Since composite insulators remain precisely unblemished in case of cut, they don’t make harm encompassing hardware and people nearby, guaranteeing most extreme security at the substation. Accordingly, significant security contemplations for power services are projected to prompt expanded inclination for combined hollow core insulators, driving the general hollow core insulators market.
On the contrary, the developing levels of power voltage are forcing expanding necessities on nature of composite hollow core insulators for substation hardware applications like transformers, breakers, flood arresters, and divider bushings. Their bigger size relates to higher assembling cost, which implies that defective units can prompt costly missteps. This is the explanation the nature of different materials that are utilized for insulator segments must be warily inspected at each creation stage. Besides, the danger of assembling mistakes as holes, voids, and territories of helpless grip between the lodging and the core should be decreased. This is by all accounts the best way to guarantee a dependably unrivaled quality interface between the lodging and the core.
Inadequate compound holding at this interface, regardless of whether restricted to a little zone, could bring about the beginning of a debasement measure, which throughout some undefined time frame could prompt disappointment. It is subsequently urgent to acquire understanding about the exhibition of defectively fortified interfaces between the silicone elastic lodging and the epoxy core, especially when presented to incomplete deliveries in a wet area.
Read Our Latest Press Release:
- https://www.prnewswire.com/news-releases/power-management-integrated-circuits-market-predicted-to-be-valued-at-us56-48-bn-by-2026–applications-in-highly-lucrative-automotive-consumer-electronics-sectors-evident-of-monumental-growth–tmr-301262055.html
- https://www.prnewswire.com/news-releases/rising-trend-of-remote-work-due-to-covid-19-pandemic-will-breathe-fresh-air-of-growth-across-the-endpoint-detection-and-response-edr-market-says-tmr-301266666.html